Value Your Building By Maintaining It’s Top Notch Condition
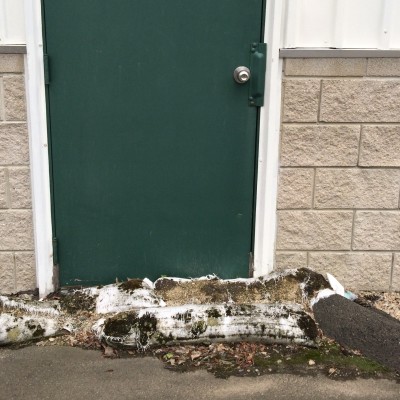
Managing deferred maintenance reduces costly capital expenditures.
Building Maintenance includes preventive maintenance, normal repairs, replacement of structural components and other work that enable facilities to consistently serve and achieve their expected life. Upgrades for serving new needs from the original design are budgeted separately. Deferred Maintenance includes work that is delayed to some future time in order to save costs, meet budget levels, or realign available dollars. The Goal Buildings should be maintained in their Certificate Of Occupancy state throughout their lifetime. Funding and proactively managing maintenance will minimize an overwhelming deferred maintenance backlog. Creative building owners find ways to fund every maintenance repair need soon after detection. Business Problem A growing backlog of postponed projects, neglected repair and ignored preventive maintenance results in a costly, complex problem. As building deterioration increases, its repairs become more challenging while costs compound. Research shows that acting only when a crisis occurs results in building owners paying considerably more than if they were consistent in their building management practices. “Every $1 in deferred maintenance costs $4 of capital renewal needs in the future,” said Rick Biedenweg, President of Pacific Partners Consulting Group. According to David Tod Geaslin’s Inverse-Square Rule for Deferred Maintenance, “If a necessary repair is deferred and allowed to remain in service until the next level of failure, the resultant expense will be 30-times the early intervention cost.”
Negative Impacts of Deferred Projects
- Safety risks and comfort issues
- Performance obstacles
- Worsening conditions e.g. A leaky roof creates a bigger problem if water damage repairs and mold remediation is necessary after the roof is repaired.
- Funding problems as deferred maintenance backlogs reach unmanageable levels.
- Lost internal support and negative public perception affect long-term construction goals.
Root Cause Analysis – Deferred maintenance happens for a variety of reasons.
- Budget constraints
- Staffing levels
- Employees do not have the necessary expertise
- Maintenance would interrupt business operations
- Willingness to wait for future renovations
Solution Champions use informed, persuasive techniques to present a business case so that management acquires ownership of the problem. They use past examples to prove the significance of escalating long-term costs due to deferred maintenance. The most convincing argument against deferred maintenance includes its risk potential for liability and safety issues, along with productivity and operational impacts.
- Prioritize projects and develop a strategy to secure adequate funding
- A facility assessment will discover the scope of the deferred maintenance problem so projects can be executed in a synergistic, prioritized, orderly and cost-effective manner. It is wise to hire a third party to evaluate the building’s repair history, condition and code compliance, as well as the performance and age of all finishes and systems.
- Suggest a better plan for the future.
- Quantify the financial impact of deferred maintenance.
- Understand why past projects, maintenance, and repairs have been deferred?
- Currently critical projects with health, safety or business continuity implications require immediate action. Additional criteria include protecting the building envelope, updating aesthetics, and boosting productivity and tenant retention/attraction.
- Potentially critical projects will become critical if not correctly planned. Energy efficiency projects to upgrade lighting, heating and cooling systems may qualify for rebates or grants. The money saved can fund more repair projects and decrease the deferred maintenance backlog.
- Necessary projects prevent downtime, damage and higher costs if they were deferred further.
- Conduct preventive maintenance and promptly complete repairs. Along with monthly checklist reviews consider seasonal actions such as servicing the HVAC system each spring along with power washing the exterior, servicing the sprinkler system, replacing air filters, grounds maintenance, exterior mold growth, foundation repair, siding repair and other tasks.
Positive Results Planned preventive maintenance enables smart management of the repair backlog and eliminates the extra costs associated with deferred repairs. This will reduce total cost of ownership and deferred maintenance backlog growth while optimizing facility condition and value.
- Category: Tech Tips, Interesting Topics
- Service: Renovation, Building Makeover, Building Renewal, Maintenance