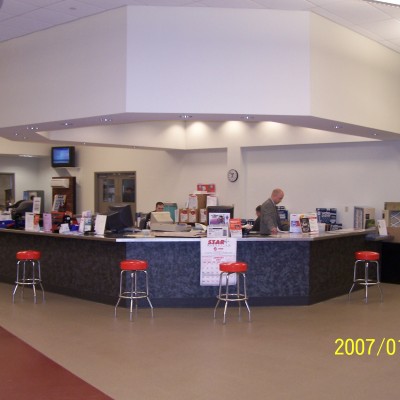
State-of-the-Art aesthetic design and functionality.
New Commercial Construction in New Haven, CT
The Business Situation
The Star Supply Company, a wholesale distributor of HVAC and refrigeration equipment, came to Munger with the need for a General Contractor in CT to build them a new business facility. The company’s current 112,000 sq.-foot headquarters and distribution center had reached its expansion limits. The owner of the company, Larry Cohen, had purchased a 25-year-old warehouse, tasking Munger to renovate and modify it for new use as a pleasant, functional, and easy-to-navigate multi-purpose work environment.
The Challenge
With an outdated warehouse facility, Munger Construction was faced with many renovation challenges in order to complete the project. As always, Munger was able to find feasible solutions to the issues at hand to get the job done on time and within budget. Major components of the renovation included refinished floors, a new showroom, and a new vestibule for welcoming visitors. A notable feature was a new 20,000 sq.-foot structure built inside the old building to satisfy requirements for offices, a showroom, a training facility, a large kitchen, and conference rooms.
The Solution
Cohen said “Munger was very organized and made sound recommendations. They saved us over $1 million from buying materials in bulk for use over the 7-month project and by repairing rather than replacing the roof. Their wonderful people are always available, timely and show personal concern. It’s not just a job to them. The project manager brings lots of experience and frequently offered worthwhile quick-hitting suggestions.”
• Temporary heat kept sprinkler systems from freezing and workers comfortable during construction.
• Concrete slabs were rehabbed. Pipes and ceilings were scraped and painted. Floors were refinished.
Old shelving was gutted. “I was impressed with Munger’s dust control measures”, said Cohen.
• A new superstructure, built inside the old building, satisfied new 20,000 sq.-feet mezzanine load
requirements for offices, showroom, training facility, large kitchen and conference rooms.
• 26 new skylights and sensor-activated lighting earned an energy conservation rebate.
• Large windows overlook the entrance and parking lot. New overhangs and matching windows convey an
original look. A creatively shaped vestibule welcomes visitors. The curved “Feature Wall,” built to tight
tolerances, presents the Star history through photos, graphics and captions.
• The showroom is highlighted by cabinetry, epoxy floors, demonstration area, self-service displays, partitioned
offices, conference room, secure area for night pick-ups and a sales counter with 13 built-in desks.
• Temporary carpeting enabled Star to open on time. It was upgraded later without business interruption.
The Result
The end product of the renovated facility provided Star Supply with measurable results across all business aspects. “People want to associate with successful businesses. Our new 165,000 sq-foot headquarters and distribution center conveys this to customers and employees”, said Cohen. “Compared to competitors who operate through distributed offices, this centralized operation yields significant advantages for Star”.

An Effective Team
– Owner, Architect, Builder, Subcontractors –
According to Art Ratner of Ratner Architects, “Munger was easy to do business with, caring, responsive and passionate about what they were doing. My client was very responsive to their suggestions. They had a very nice working relationship and mutual understanding. A fair exchange on both sides, when negotiating change orders, puts people at ease. Joe Pierandi, project manager, did a superb job of staying on top of everything and was always available for us. Munger completed a number of punch list finishing touches without interrupting business operations. I am delighted with their responsiveness when we need them to return for a particular issue that we discover after-the-fact.”
Cohen said “Munger was very organized and made sound recommendations. They saved us over $1 million from buying materials in bulk for use over the 7-month project
and by repairing rather than replacing the roof. Their wonderful people are always available, timely and show personal concern. It’s not just a job to them. The project manager brings lots of experience and frequently offered worthwhile quick-hitting suggestions.”
Measurable Business Results from a Renovated
“People want to associate with successful businesses. Our new 165,000 sq-foot headquarters and distribution center conveys this to customers and employees”, said Cohen. “Compared to competitors who operate distributed offices, this centralized operation yields significant advantages for Star.”
- Happy and productive employees
- Enhanced communications between departments
- Logical, efficient workflow improves worker output
- 12 loading docks for simultaneous shipping and receiving
- Organized layouts and bar coding to manage inventory
- State-of-the-art training facility builds dealer channel
- Attract and retain the best employees
- Expanded product offerings retain and grow customers
- Secure night pick-up and will-call services enable
contractors to be in and out in 6 minutes
Munger’s Role
“Munger won this competitive bid due to the professional way in which they conducted themselves during their proposal review with the owner”, said Ratner.
After helping Cohen to determine that the building was a good one to buy, Munger performed many roles throughout the project.
“It was like building a million dollar house”, said Pierandi. “We worked closely with the architect and interior, furniture and cabinetry designers, and mechanical engineers. We were involved with the people who installed elaborate heating and cooling systems and with the security system team to get doors and locksets correct.”
As general contractor Munger managed all subcontractors.
Munger craftsmen installed doors and hardware, and provided general carpentry and cabinetry services. They built the large U-shaped stainless steel showroom counter tops.
“You can’t beat the economies of renovating an old building compared to building a new one”, said David DeMaio, Munger president.
“Munger’s Subcontractors
were fabulous, said Cohen. I attribute this to Munger’s selection process, tenured relationships, and teamwork.”
- Tenedine Construction – site work
- Caplow Mechanical – plumbing and fire protection
- CM Crocco – HVAC
- Massey Glass – glass and glazing
- Empire Drywall – ceilings and dry wall
- Rte 80 Lumber and Millwork – cabinetry
- Floors and More – carpet, tile and wood flooring
- ICS – slab coating for warehouse and showroom
- RA Torre – office & warehouse paint and wallpaper